Flange para tubulação industrial: como escolher e utilizar corretamente
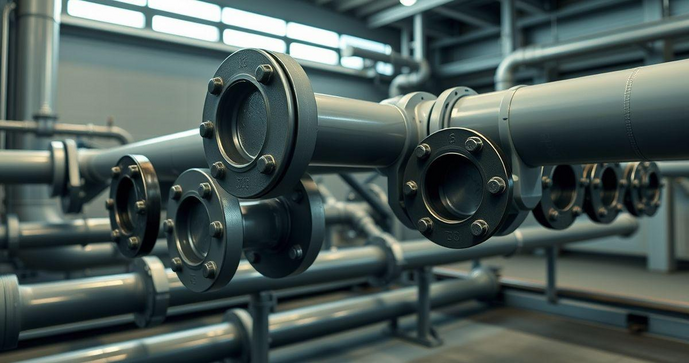
Principais Tipos de Flanges e Suas Aplicações
As flanges são componentes cruciais em sistemas de tubulação, utilizadas para realizar conexões entre tubações, equipamentos e válvulas. Existem diversos tipos de flanges, cada um projetado para atender a necessidades específicas. Conhecer as principais variedades e suas aplicações é fundamental na escolha adequada para seu projeto industrial.
Flange de Solda: Este tipo de flange é muito utilizado em sistemas de alta pressão, pois oferece uma conexão robusta. Normalmente, as flanges de solda são fixadas diretamente na tubulação por meio de um processo de soldagem, proporcionando uma vedação eficaz e resistente. São comuns em indústrias químicas e petroquímicas onde a segurança e a integridade nas conexões são prioritárias.
Flange de Parafuso: Também conhecida como flange de ângulo, este modelo é fixado por meio de parafusos, facilitando a desmontagem e manutenção de sistemas tubulares. Geralmente, essas flanges são utilizadas em sistemas que não requerem alta pressão, como em indústrias alimentícias ou em sistemas de água. A vantagem é a facilidade na instalação e no acesso aos componentes internos.
Flange Cega: Comumente utilizada em extremidades de tubulações, a flange cega não possui furo e é utilizada para fechar extremidades, evitando vazamentos. Adequada para sistemas onde não se espera a circulação de fluidos nos pontos de fechamento, é amplamente aplicada em sistemas hidráulicos e de ventilação.
Flange de Juntas Metálicas: Esse tipo permite a utilização de uma junta metálica entre as superfícies de vedação e é ideal para suportar altas temperaturas e pressões. Elas são frequentemente empregadas em indústrias que lidam com vapor ou gases a altas temperaturas, garantindo a vedação necessária sem comprometer a estrutura.
Flange de Acoplamento: Utilizada para conectar tubos de diferentes diâmetros, a flange de acoplamento permite a expansão e a contração da tubulação, facilmente ajustando-se às necessidades das instalações. É ideal para aplicações que envolvem mudanças frequentes de layout, como no setor de construção ou em usinas de energia.
Em resumo, selecionar o tipo correto de flange levando em consideração suas aplicações, pressão e tipo de fluido é crucial para garantir a eficiência e a segurança do sistema de tubulação. Conhecer as características de cada tipo de flange ajuda os engenheiros e técnicos a tomar decisões mais informadas durante o planejamento de projetos industriais.
Critérios para Seleção da Flange Ideal
A seleção da flange ideal para um sistema de tubulação é uma etapa fundamental que deve ser realizada com cuidado. Existem diversos critérios que devem ser considerados para garantir a segurança e eficiência da instalação. Aqui estão os principais aspectos a serem avaliados ao escolher a flange apropriada.
1. Tipo de Material: O material da flange deve ser compatível com os fluidos que irão passar pelo sistema. Flanges de aço inoxidável são utilizadas em ambientes corrosivos, enquanto flanges de aço carbono são comuns em aplicações menos agressivas. É importante considerar fatores como resistência química e temperatura para evitar falhas e desgastes prematuros.
2. Pressão e Temperatura de Operação: Cada flange tem uma especificação de pressão e temperatura máxima que deve ser respeitada. A flange escolhida deve suportar as condições operacionais do sistema para evitar vazamentos e falhas. Consultar as normas da indústria, como ASME, pode oferecer diretrizes úteis para a seleção.
3. Norma e Padrão: Flanges podem seguir diferentes normas e padrões, como ANSI, API e DIN. A escolha da flange deve estar alinhada aos padrões que governam o projeto do sistema, garantindo que todas as partes sejam compatíveis e atendam aos requisitos técnicos necessários.
4. Tipo de Conexão: Considerar o método de conexão da flange é essencial. Dependendo do sistema instalado, flanges de solda, parafuso ou juntas podem ser mais apropriadas. Flanges de solda oferecem maior resistência, enquanto as de parafuso podem facilitar manutenções futuras.
5. Espessura e Dimensões: A espessura da flange e suas dimensões devem ser compatíveis com o diâmetro da tubulação e com as condições de operação. Flanges muito finas podem não suportar a pressão esperada, enquanto flanges excessivamente grossas podem adicionar peso desnecessário ao sistema.
6. Condições Ambientais: O ambiente onde a flange será instalada também é crucial. Fatores como umidade, presença de produtos químicos, temperatura e vibrações ambientais podem influenciar a escolha do material e do tipo de flange. Para ambientes agressivos, flanges com revestimentos especiais podem ser necessárias.
Considerar esses critérios ajudará a garantir que a flange não apenas atenda às necessidades operacionais, mas também contribua para a segurança e a durabilidade de todo o sistema de tubulação. A escolha cuidadosa da flange ideal pode prevenir problemas futuros e garantir o funcionamento eficiente da instalação.
Processo de Instalação de Flanges em Tubulações
A instalação de flanges em tubulações é um processo que requer atenção a detalhes e seguir normas específicas para garantir a segurança e a eficácia do sistema. Aqui está um passo a passo do processo de instalação de flanges, desde a preparação até a fixação final.
1. Preparação do Local: Antes de iniciar a instalação, é essencial preparar o local onde as flanges serão montadas. Isso envolve a limpeza das superfícies de vedação das flanges e das extremidades das tubulações, removendo qualquer sujeira, óleo ou detritos que possam interferir na vedação correta.
2. Verificação das Dimensões: Certifique-se de que as flanges escolhidas estão de acordo com as dimensões das tubulações. O alinhamento correto é crucial para evitar tensões indesejadas nas flanges e garantir uma vedação eficiente.
3. Colocação da Junta de Vedação: Se as flanges necessitam de juntas de vedação, posicione a junta corretamente entre as superfícies das flanges. A escolha da junta deve ser apropriada para o tipo de fluido e as condições de operação. Juntas de borracha, fibra ou metal são algumas opções disponíveis.
4. Alinhamento das Flanges: Posicione as flanges de forma que os furos dos parafusos coincidam. Isso evitará desalinhamentos durante a fixação e ajudará a manter a integridade do sistema. Um alinhamento adequado é fundamental para garantir que a pressão não cause falhas nas juntas.
5. Fixação através de Parafusos: Se estiver utilizando flanges de parafuso, insira os parafusos ou porcas nos furos correspondentes. Aperte os parafusos em um padrão cruzado para garantir uma distribuição uniforme da pressão. Isso ajuda a evitar que uma flange se deforme devido a tensões excessivas.
6. Teste de Estanqueidade: Após a instalação, realize um teste de estanqueidade para verificar se há vazamentos. Este teste é fundamental, especialmente em sistemas que transportam fluidos pressurizados. Observe qualquer sinal de vazamento ao redor das flanges e realize os ajustes necessários.
7. Inspeções Regulares: Após a instalação, é recomendado programar inspeções regulares para verificar o estado das flanges e as juntas. Isso garante que quaisquer problemas sejam identificados e corrigidos antes de se tornarem sérios, aumentando a durabilidade do sistema de tubulação.
Seguir esse processo de instalação com atenção contribuirá para uma conexão segura e eficiente nas tubulações. A qualidade da instalação das flanges é crítica para o desempenho geral e a segurança do sistema industrial.
Cuidados e Manutenção de Flanges em Sistemas Industriais
A manutenção adequada das flanges em sistemas industriais é essencial para garantir a eficiência e a segurança das operações. Vários cuidados devem ser tomados para evitar problemas e prolongar a vida útil das flanges. A seguir, apresentamos algumas diretrizes para a manutenção e o cuidado com flanges em tubulações.
1. Inspeções Regulares: Realizar inspeções periódicas é fundamental para identificar sinais de desgaste ou deterioração. Verifique se há vazamentos ao redor das flanges, cracks, corrosão ou qualquer outro dano. A detecção precoce pode evitar falhas maiores e interrupções no sistema.
2. Limpeza das Flanges: A sujeira e resíduos podem acumular-se nas flanges e nas juntas, prejudicando a vedação. Periodicamente, limpe as superfícies de vedação e as flanges utilizando um pano seco ou um produto de limpeza apropriado. Evite o uso de materiais abrasivos que possam danificar as superfícies.
3. Verificação da Torque dos Parafusos: Ao longo do tempo, os parafusos que fixam as flanges podem se afrouxar devido à vibração ou mudanças de temperatura. Verifique a tensão dos parafusos e aplique torque conforme recomendado. Isso assegura que a vedação permaneça eficiente e evita vazamentos.
4. Monitoramento de Condições Operacionais: Mantenha um registro das condições operacionais do sistema, incluindo pressão e temperatura. Flanges projetadas para altas pressões podem não funcionar adequadamente em condições que excedem suas especificações. Ajustar as operações dentro dos limites seguros é crucial para a longevidade das flanges.
5. Substituição de Juntas: As juntas utilizadas entre as flanges podem se desgastar com o tempo. Ao realizar uma manutenção ou inspeção, verifique se as juntas ainda estão em bom estado. Juntas comprometidas devem ser substituídas imediatamente para prevenir vazamentos e falhas no sistema.
6. Treinamento da Equipe: A equipe responsável pela manutenção deve ser treinada adequadamente sobre os tipos de flanges e as especificidades de cada sistema. O conhecimento sobre como realizar inspeções, manutenções e reparos garante uma abordagem eficaz na preservação da infraestrutura.
7. Documentação e Registro: Manter registros detalhados de todas as manutenções realizadas, incluindo datas, inspeções e substituições, é fundamental. Essa documentação ajudará a monitorar a condição das flanges ao longo do tempo e guiará em futuras decisões de manutenção.
Em suma, seguir essas diretrizes de cuidado e manutenção das flanges em sistemas industriais é crucial para assegurar seu funcionamento adequado e minimizar riscos operacionais. Uma boa gestão das flanges pode aumentar a eficiência e a segurança das operações, beneficiando toda a instalação industrial.
Benefícios do Uso de Flanges para Conexões Industriais
O uso de flanges para conexões industriais oferece uma série de benefícios que contribuem para a segurança e eficiência de sistemas de tubulação. Este componente é essencial em diversas aplicações industriais, e entender suas vantagens pode auxiliar na escolha adequada para projetos. A seguir, destacamos os principais benefícios do uso de flanges.
1. Facilidade de Manutenção: As flanges permitem a desmontagem rápida e fácil de sistemas de tubulação. Isso facilita a manutenção e a inspeção de equipamentos, reduzindo o tempo de inatividade e os custos operacionais. Durante a manutenção, é possível acessar rapidamente componentes internos sem comprometer toda a estrutura da tubulação.
2. Versatilidade: Flanges estão disponíveis em uma ampla variedade de tipos, tamanhos e materiais, tornando-as adequadas para diferentes aplicações e ambientes operacionais. Essa versatilidade permite que as flanges sejam utilizadas em diversos setores, como químico, petroquímico, farmacêutico e de água.
3. Confiabilidade nas Conexões: Flanges proporcionam conexões seguras e estanques, minimizando o risco de vazamentos. Quando instaladas e mantidas corretamente, elas garantem a integridade do sistema e a segurança operacional, especialmente em ambientes que lidam com substâncias perigosas.
4. Redução de Custos a Longo Prazo: Embora a aquisição inicial de flanges possa representar um investimento, sua durabilidade e facilidade de manutenção podem resultar em economia significativa. Com flanges de qualidade, a necessidade de reparos frequentes e substituições é reduzida, resultando em menor custo total de propriedade ao longo do tempo.
5. Adaptabilidade a Diferentes Condições: Flanges podem ser projetadas para suportar uma ampla gama de pressões e temperaturas, tornando-as adequadas para sistemas que operam em condições extremas. Essa adaptabilidade é crucial em indústrias que requerem alto desempenho sob estresse.
6. Conformidade com Normas e Padrões: O uso de flanges que seguem normas industriais reconhecidas, como ASME ou ANSI, garante que as conexões atendam aos padrões de segurança e desempenho exigidos. Isso é especialmente importante em aplicações que envolvem regulamentações rigorosas.
7. Integração com Sistemas de Automação: Com a crescente adoção de tecnologias de automação industrial, flanges podem ser facilmente integradas em sistemas que utilizam sensores e monitoramento remoto. Isso permite um controle mais eficiente do sistema de tubulação, facilitando a detecção de problemas e a manutenção preditiva.
Em resumo, o uso de flanges nas conexões industriais oferece uma série de benefícios, incluindo facilidade de manutenção, confiabilidade, versatilidade e customização para diversas condições operacionais. A escolha de flanges de qualidade pode melhorar significativamente o desempenho e a segurança dos sistemas de tubulação, tornando-se uma decisão estratégica em projetos industriais.
Tendências e Inovações em Flanges para Tubulações
O setor industrial está em constante evolução, e a tecnologia relacionada às flanges para tubulações não é exceção. Novas tendências e inovações surgem continuamente, visando melhorar a eficiência, a segurança e a sustentabilidade dos sistemas de tubulação. A seguir, destacamos algumas das principais tendências e inovações no uso de flanges.
1. Materiais Avançados: O desenvolvimento de novos materiais, como ligas metálicas de alta resistência e compósitos, está transformando a fabricação de flanges. Esses materiais oferecem melhor resistência à corrosão e temperaturas extremas, aumentando a durabilidade e vida útil das flanges em ambientes desafiadores.
2. Flanges Inteligentes: Com o avanço da Internet das Coisas (IoT), flanges inteligentes estão se tornando uma realidade. Equipadas com sensores, essas flanges podem monitorar pressão, temperatura e vazamentos em tempo real, alertando os operadores sobre condições anormais e permitindo ações corretivas rápidas.
3. Sustentabilidade: A busca por soluções mais sustentáveis está influenciando a produção de flanges. Empresas estão adotando práticas de fabricação que reduzem o desperdício e utilizam materiais recicláveis. Além disso, flanges que suportam fluidos sustentáveis, como biocombustíveis, estão se tornando mais comuns.
4. Personalização e Modularidade: A personalização das flanges para atender a requisitos específicos de cada projeto está ganhando popularidade. Flanges modulares permitem a adaptação e redesign de sistemas de tubulação de forma mais eficiente, atendendo a necessidades específicas sem comprometer a funcionalidade.
5. Aumento na Automação: A automação industrial está impactando a forma como as flanges são instaladas e mantidas. Sistemas automatizados estão sendo utilizados para a montagem de flanges, garantindo precisão e reduzindo o trabalho manual. Isso também contribui para a consistência na qualidade das conexões.
6. Normas e Certificações: Novas regulamentações e padrões estão sendo estabelecidos para segurança e eficiência em sistemas de tubulação. Isso leva à criação de flanges que atendem a requisitos rigorosos, assegurando a confiabilidade das conexões em indústrias sensíveis, como farmacêuticas e de energia.
7. Integração com Sistemas de Controle: Flanges estão se tornando uma parte integrante de sistemas de controle industrial. Ao integrar flanges com tecnologia de automação, é possível melhorar a gestão de sistemas de tubulação, facilitando o monitoramento e a manutenção preventiva, o que resulta em operações mais seguras e eficientes.
Essas tendências e inovações em flanges para tubulações não apenas atendem às demandas atuais da indústria, mas também preparam o caminho para o futuro das conexões industriais. Com a contínua evolução da tecnologia, espera-se que as flanges desempenhem um papel ainda mais crucial na segurança e eficiência das operações industriais.
Em conclusão, a escolha e o uso adequados de flanges para tubulações são fundamentais para garantir segurança, eficiência e durabilidade nos sistemas industriais. Ao considerar os diferentes tipos de flanges, critérios de seleção, processos de instalação e manutenção, é possível otimizar o desempenho das tubulações e minimizar riscos operacionais.
Além disso, estar atento às tendências e inovações do setor contribui para a implementação de soluções mais seguras e sustentáveis.
Investir tempo e recursos na seleção e no cuidado com flanges não é apenas uma necessidade técnica, mas uma estratégia que pode resultar em significativas economias e melhorias na eficiência operacional. A compreensão dessas práticas é essencial para profissionais e empresas que buscam excelência em suas operações industriais.
Gostou? compartilhe!
Gostou? compartilhe!